背景技术:
在目前石油化工行业的装置检维修中,盛行推出法兰检修中螺栓实现定力矩紧固的要求,从而引起了定扭矩扳手的推出市场。由于在施工中要求能够实现高精度的定扭矩,因此需要使用专用的扭矩测试工具来测出扭矩扳手的实时扭矩。
根据目前的市场调查,大多数的扭矩测试平台都是一端设有反作用力臂支撑块,然后扳手的反作用力臂靠在该支撑块上进行扳手扭矩测试,这种方式在测试过程中会导致电动扭剪扳手的反作用力臂中出现弯矩,从而无法达到高精度测量,并且还会出现数据跳动大、不稳定的现象。再者,现有的扭矩测试平台的外形体积和质量都比较笨重、体积大、加工成本高,只适用于厂房固定位置的测试,不便于移动或更换位置,测试比较死板,从而给使用者带来了诸多的不便。
技术实现要素:
本实用新型在于针对现有技术存在的缺陷与不足,提供一种便捷的扭矩扳手测试平台,可实现测试精度高、加工成本低以及轻便灵活得要求。
为实现上述目的,本实用新型提供的电动扭剪扳手扭矩测试平台,包括:
底框架,底框架的底部设有圆孔,并在圆孔中设有键槽,底框架的两相对侧边均设有固定槽;
扭矩传感器,所述扭矩传感器的一端套接在所述底框架的圆孔中;
转接工装,所述转接工装的底端设有第二圆孔,第二圆孔中设有第二键槽,第二圆孔与扭矩传感器的另一端套接,转接工装的顶端内设有孔位,用于与待测扳手输出轴连接;
电动扭剪扳手反作用力臂,所述电动扭剪扳手反作用力臂的两端均设有两个凸起,分别卡在底框架的两侧的u型槽上,并在与转接工装顶端孔位对应处设有第二孔位;
其中,待测扳手的输出轴穿过第二孔位,并与孔位配合连接。
进一步的,所述底框架包括侧板、第二侧板、底板和支撑钢板,所述侧板和第二侧板沿底板呈对称布置,所述固定槽分别设在所述侧板和第二侧板的上方,所述圆孔位于所述底板的,所述支撑钢板焊接在所述底板的底部端面上,作为整个测试平台的支撑腿。
进一步的,所述侧板和第二侧板均设有三角板进行支撑。
进一步的,所述固定槽为u型槽。
进一步的,所述扭矩传感器的两端分别设有卡位键和第二卡位键,所述卡位键与键槽配合固定。
进一步的,所述扭矩传感器的一端通过轴套与圆孔固定。
进一步的,所述转接工装的第二键槽与扭矩传感器的第二卡位键配合固定。
进一步的,所述转接工装的中间设为中空状,用于减轻自身的重量。
进一步的,所述第二孔位与待测电动扭剪扳手的输出轴形状匹配。
使用时,将电动扭剪扳手的输出轴穿过并卡在电动扭剪扳手反作用力臂的第二孔位内,再将电动扭剪扳手反作用力臂的两端的凸起卡在u型槽内,将电动扭剪扳手的输出轴转接工装上的孔位配合安装,启动电动扭剪扳手,进行测试即可。
与现有技术相比,本实用新型的有益效果在于:
通过本实用新型特定设有的对反作用力臂的两端均进行支撑的支撑块,从根本上了以前测试过程中出现的电动扭剪扳手的反作用力臂中存在的弯矩的问题,从而提高了测试精度,并减少甚避免了数据跳动大、不稳定的现象;且本实用新型的电动扭剪扳手测试平台测试灵活、制作成本低、体积小、便于移动;另一方面,本实用新型的电动扭剪扳手测试平台能覆盖多规格的扳手测试,便于对不同规格的扳手进行测试,提高测试效率。
附图说明
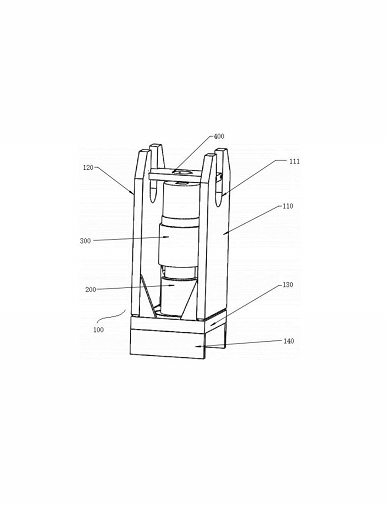
附图标记说明:
100、底框架;110、侧板;111、u型槽;120、第二侧板;130、底板;131、键槽;140、支腿钢板;200、扭矩传感器;210、卡位键;220、第二卡位键;300、转件工装;310、第二键槽;320、孔位;400、电动扭剪扳手反作用力臂;410、第二孔位;500、轴套;600、电动扭剪扳手。
具体实施方式
为了更了解本实用新型的技术内容,特举具体实施例并配合所附图式说明如下。
在本公开中参照附图来描述本发明的各方面,附图中示出了许多说明的实施例。本公开的实施例不必定意在包括本发明的所有方面。应当理解,上面介绍的多种构思和实施例,以及下面更加详细地描述的那些构思和实施方式可以以很多方式中任意一种来实施。
结合图1所示,本实施例提供的便捷的电动扭剪扳手测试平台,包括底框架100、扭矩传感器200、转接工装300和电动扭剪扳手反作用力臂400。
结合图1、2所示,底框架100由侧板110,第二侧板120,底板130和支腿钢板140焊接而成,侧板110和第二侧板120的外形尺寸一样,沿底板130呈对称焊接,并用三角板支撑,且都设有u型槽111,用来安装电动扭剪扳手反作用力臂400,底板130的设有圆孔,并在圆